Securing Critical Components for Rapid Innovation
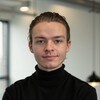

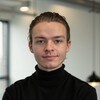
Building a Resilient Supply Chain: Securing Critical Components for Rapid Innovation
As we scale our rapid-prototyping microfactory to meet growing demand, the fragility of global supply chains has become front and center. In this post, we dive deep into the strategies, tools, and partnerships that CriusCo has put in place to ensure continuous access to the critical components that power our hardware R&D—and to translate volatile markets into a competitive advantage.
I. The Supply-Chain Headwinds in Hardware R&D
Over the past few years, we’ve seen:
- Global chip shortages driven by pandemic-related factory shutdowns and surging demand
- Logistics bottlenecks, from port congestion to container shortages
- Single-source dependencies, where one vendor holds sway over a key part
These challenges can halt prototype builds, delay field trials, and drive up costs unpredictably. At CriusCo, we knew we needed a holistic, data-driven approach to turn these headwinds into tailwinds for innovation.
II. Our Multi-Pronged Mitigation Strategy
-
Dual-Sourcing & Tiered Vendor Networks
- At project kickoff, every long-lead item is qualified with at least two independent suppliers.
- We maintain a “Tier 1” preferred vendor list for performance and a “Tier 2” backup list for rapid cut-over.
- Quarterly vendor audits ensure backup partners can meet our quality and volume requirements.
-
Micro-Fulfillment Hubs
- Regional stock buffers located in Detroit, Tallinn, and our Asia partner sites hold critical inventory on consignment.
- These hubs leverage local carriers and bonded warehouses to accelerate last-mile delivery.
- We refresh hub inventory weekly based on live consumption metrics and lead-time forecasts.
-
Safety-Stock Analytics
- A custom reorder algorithm balances holding costs against risk exposure, dynamically adjusting point-of-order and order quantities.
- Machine-learning models ingest historical lead times, supplier performance, and macro-economic indicators to predict delays.
- Alerts trigger early manual reviews when projected delivery slippage exceeds defined tolerances.
III. Digital Visibility & Real-Time Tracking
- Vendor Portal Integration
- Our procurement system ties directly into supplier EDI feeds and REST APIs to surface PO acknowledgements, shipment ETAs, and exception alerts in real time.
- IoT-Enabled Inventory
- RFID tags on all critical reels and palletized parts, combined with low-power LoRaWAN readers in our hubs, deliver continuous bin-level counts.
- Supply-Chain Dashboard
- Live KPIs—fill-rate, days-on-hand, supplier lead-time variance—are displayed on shop-floor screens and in our remote operations center, giving every engineer and manager full transparency.
IV. Co-Engineering with Key Suppliers
Bringing vendors in early reduces surprises down the line:
- Early Design Reviews
- Joint CAD/DFX sessions identify manufacturability or sourcing challenges before the first prototype is ordered.
- Joint Risk Workshops
- Cross-functional FMEA tables with our engineering, quality, and procurement teams uncover potential failure modes and mitigation plans.
- Vendor R&D Program
- We fund small-batch pilot runs at supplier facilities to qualify novel or custom parts, sharing tooling costs and test results.
V. Case Study: Securing the Next-Gen Edge Compute Board
-
The Challenge
Our chosen SoC had a quoted 16-week lead time—unacceptable for an aggressive Q4 rollout. -
Our Tactics
- Split BOM Strategy: Divided the design into a “primary” path using the flagship SoC and a “lite” backup version on a widely available microcontroller.
- Prepaid Mask Sets: Advanced payment to two foundries to reserve next-slot manufacturing capacity.
- Phased Rollout Plan: Shipped early lite-version boards to internal teams for software integration while awaiting the full-featured units.
-
The Outcome
- Mean lead time compressed from 16 to 6 weeks.
- Seamless cut-over: no disruptions in our software integration schedule.
- Early software validation began two weeks ahead of plan.
VI. Measurable Wins & Lessons Learned
- Proactivity pays off: Early identification of risk reduces emergency air-freight premiums.
- Data transparency: Real-time dashboards turn gut-feel decisions into measurable actions.
- Partnerships matter: Co-funding pilot runs builds supplier loyalty and shared accountability.
VII. What’s Next
- AI-Driven Forecasting: We will explore how our ML-based demand models can anticipate part shortages months in advance.
- Digital-Thread Integration: We’re linking CAD revisions, supplier quotes, and shop-floor picks into a single source of truth—minimizing handoffs and errors.
- Open-Source BOM Templates: Later this year, we’ll publish our supplier-qualification checklists and EDI schemas on GitHub to help the broader community accelerate hardware development.
Building a resilient supply chain isn’t just about stacking inventory—it’s about creating a living network of visibility, partnerships, and predictive analytics that turns uncertainty into strategic advantage.